Wafer Cassette
Wafer cassettes are crucial for protecting wafers during transport and storage in semiconductor manufacturing, preventing contamination and damage. They facilitate wafer handling in production, widely used in semiconductor fabs and solar cell manufacturing. Available in sizes like 200mm and 300mm, metal wafer cassettes provide durability, while plastic options like teflon are lightweight and corrosion-resistant.
- Durable materials
- Precise Dimensions
- High cleanliness standards
- Competitive pricing
- Supports Small Batch Custom Production
What is Wafer Cassettes?
Wafer cassettes are specialized containers designed to safely hold and transport semiconductor wafers during the manufacturing process. These cassettes are crucial in the semiconductor industry, as they protect delicate wafers from contamination, physical damage, and environmental factors.
Typically made from durable materials like polypropylene or aluminum, wafer cassettes feature compartments that securely hold individual wafers to prevent movement and minimize the risk of scratches. They come in various sizes to accommodate different wafer diameters, such as 200mm and 300mm, and can be customized to meet specific requirements.
In addition to their protective role, wafer cassettes are engineered to resist a wide range of industrial chemicals and solvents, ensuring their usability in diverse processing environments. Their design also facilitates efficient transportation between processing stations, helping to streamline production workflows.
Overall, wafer cassettes are essential for maintaining the integrity of semiconductor wafers, contributing significantly to the efficiency and effectiveness of the fabrication process.
By Wafer Cassettes Material
By Wafer Cassette Dimensions
By Wafer Cassette Application
(I) Semiconductor Manufacturing Processes
1. Lithography Process
Lithography is a core process in semiconductor manufacturing, and its precision directly determines the performance of chips. Before lithography, the wafer cassette is responsible for accurately transporting wafers from the storage area to the lithography machine. It features an ultra-clean sealing design combined with a HEPA high-efficiency filtration system, which can limit particulate contaminants entering the chamber to no more than 10 particles of 0.1 micrometers or smaller per cubic meter (meeting ISO Class 1 cleanliness standards). This prevents dust and impurities from adhering to the wafer surface, avoiding defects in lithography patterns. During transportation, the high-precision positioning slots of the wafer cassette ensure that the wafer position error is less than ±50 micrometers, enabling seamless docking with the lithography machine’s robotic arm and preventing pattern distortion caused by wafer misalignment. After lithography, the photoresist coated on the wafer surface is extremely fragile. The wafer cassette uses shock-absorbing structures and electrostatic dissipative materials to effectively absorb transportation vibrations and eliminate electrostatic damage to the photoresist, safeguarding the integrity of the lithography patterns.
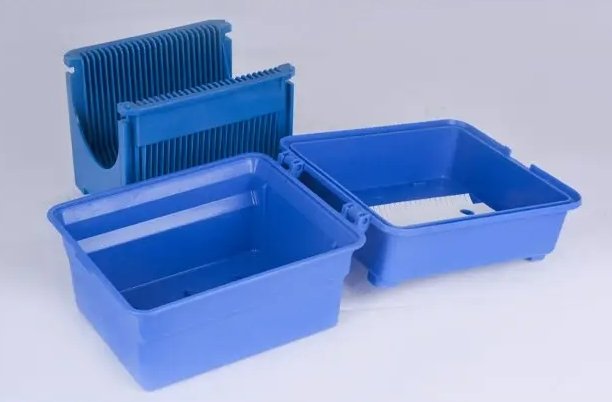
2. Etching Process
3. Thin Film Deposition Process
Thin film deposition requires the wafer surface to be absolutely clean to ensure the uniformity and adhesion of the thin film. Before entering the deposition equipment, the wafer cassette undergoes real-time monitoring of internal particle concentration, temperature, and humidity through an online cleanliness detection system. It is only allowed to dock with the deposition equipment once the indicators meet the standards. Its nitrogen purging function can replace the internal air with high-purity nitrogen before loading wafers, reducing the content of oxygen and water vapor and preventing wafer oxidation. After deposition, since thin films are usually only a few nanometers thick and extremely fragile, the wafer cassette adopts low-stress loading technology. The air pressure buffer device reduces the impact force during wafer loading, and the darkroom light-shielding design prevents chemical reactions of the thin film caused by light exposure, ensuring the stability of the thin film’s performance.
(II) Wafer Transportation and Storage
1. Internal Transportation in Wafer Fabs
Inside the cleanrooms of wafer fabs, wafer cassettes need to be frequently transferred between different equipment. Their AGV (Automated Guided Vehicle) compatible interfaces can seamlessly connect with the factory’s automated transportation system, enabling unmanned and precise transportation. Meanwhile, RFID (Radio-Frequency Identification) tags can track the position and status of wafers in real-time, avoiding transportation errors. In addition, the integrated temperature and humidity sensors in the wafer cassette will immediately trigger an alarm and activate the emergency protection program once environmental parameters deviate during transportation, ensuring that wafers remain in a stable environment.
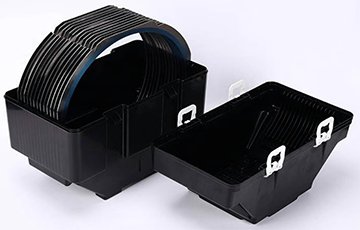
2. Transportation between Wafer Fabs and Packaging Facilities
During long-distance transportation, wafer cassettes must withstand challenges such as vibrations and changes in temperature and humidity. Their anti-vibration buffer structures, made of honeycomb polymer materials, can absorb over 90% of vibration energy. The constant temperature and humidity chambers can limit internal temperature fluctuations to ±1°C and maintain humidity between 30% – 40% RH. Equipped with GPS positioning and real-time monitoring systems, the entire transportation process can be visualized, ensuring the safe arrival of goods at their destination.
3. Long-Term Storage
Long-term storage requires wafer cassettes to have excellent anti-oxidation and moisture-proof capabilities. Their vacuum sealing technology can reduce the internal air pressure to below 10^-3 Pa. Combined with the automatic desiccant regeneration module, it can effectively isolate water vapor and oxygen. The UV-resistant outer shell can block harmful light, preventing the aging of wafer materials and ensuring stable wafer performance during long-term storage.
(III) Scientific Research and Laboratories
1. Specialized for Small-Sized Wafers
Scientific research institutions often use small-sized wafers, such as 4-inch and 6-inch wafers, for experiments, which are difficult to fit in traditional wafer cassettes. Customized products feature a modular slot design, allowing flexible adjustment of slot spacing to accommodate wafers of different sizes. Meanwhile, their high-precision weight sensors can monitor weight changes of wafers in real-time, assisting researchers in analyzing mass variations during experiments and meeting diverse experimental requirements.
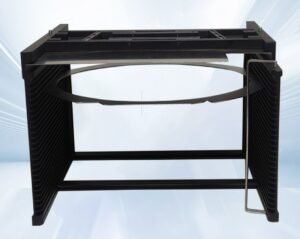
2. Adaptable to Special Experimental Environments
In special environments with extreme temperatures or strong magnetic fields, ordinary wafer cassettes cannot function properly. For such requirements, customized products use high/low-temperature resistant materials (capable of withstanding temperatures from -196°C to 500°C) and magnetic shielding structures, ensuring that wafers are unaffected in special environments and providing reliable wafer storage and transportation solutions for cutting-edge scientific research projects.
FAQs:
1. Do you provide customized wafer cassettes?
2. How to select a suitable wafer cassette according to the wafer size?
Wafer sizes mainly include 4 – inch, 6 – inch, 8 – inch, and 12 – inch. It is necessary to select a wafer cassette of the corresponding size specification. At the same time, pay attention to the spacing and depth of the slots inside the cassette, as well as the fixing method of the wafers, to ensure that the wafers are placed stably and can be taken out and placed smoothly.
3. What are the main materials of wafer cassettes? What are their characteristics?
The main materials include polycarbonate (PC), silicon carbide (SiC), and quartz, etc. Polycarbonate has the advantages of low cost and high transparency, which is convenient for observing wafers; silicon carbide has excellent high – temperature resistance, wear resistance, and anti – static performance, making it suitable for harsh process environments; quartz has extremely high chemical stability and high – temperature tolerance, and is often used in high – end wafer manufacturing.
4. How is the anti - static performance of wafer cassettes ensured?
Most wafer cassettes are made of anti – static materials or coated with an anti – static layer on the surface. Strict anti – static tests are carried out during the production process to ensure that their surface resistance values meet the semiconductor industry standards and prevent static electricity from damaging the wafers.
5. How many wafers can a wafer cassette usually hold?
The loading quantity varies depending on the wafer size and the specification of the wafer cassette. Generally, an 8 – inch wafer cassette can hold 25 wafers, and a 12 – inch FOUP can usually hold 25 – 30 wafers. For specific quantities, please refer to the product specification.
6. How to clean and maintain wafer cassettes?
When cleaning, use a cleanroom wipe and a special cleaning agent to wipe off surface stains. For stubborn dirt, ultrasonic cleaning can be used. Avoid scratching the cassette body with sharp tools. After cleaning, dry it in a cleanroom environment, and avoid contact with corrosive substances during storage.
7. Can wafer cassettes withstand high - temperature environments?
The temperature tolerance varies for different materials. Wafer cassettes made of polycarbonate generally can withstand temperatures of about 80 – 100°C; those made of silicon carbide and quartz can withstand higher temperatures, and some products can withstand temperatures above 1000°C. For specific values, please refer to the product parameters.
8. How do wafer cassettes protect wafers during transportation?
Wafer cassettes have precise slot and fixing structures inside, which can prevent wafers from shifting and colliding during transportation. At the same time, their sealed design can effectively isolate dust, moisture, and harmful gases, maintaining a clean environment inside.
9. Are there preferential policies for bulk purchases of wafer cassettes?
Bulk purchases can enjoy tiered discounts. The specific discount range depends on the order quantity, product type, and customization requirements. For details, please contact our sales team for a quote.
10. What is the delivery cycle of wafer cassettes?
Standard products are usually delivered within 7 – 15 working days; the delivery cycle of customized products will be evaluated according to the complexity, generally 20 – 45 working days. The delivery time for special customization requirements can be further negotiated.
11. Is the packaging of wafer cassettes suitable for long - distance transportation?
We adopt a multi – layer protective packaging scheme, using a sturdy carton or wooden box on the outside and matching anti – static and cushioning materials on the inside to ensure that wafer cassettes are not damaged by vibration and extrusion during long – distance transportation. At the same time, the packaging meets international transportation standards.
12. Has the product passed relevant quality certifications?
Our wafer cassettes have passed the ISO 9001 quality management system certification, and some products also comply with SEMI international semiconductor equipment and materials standards, ensuring that the product quality and performance reach the leading level in the industry.
13. How to handle it if a wafer cassette is damaged during use?
If there is non – man – made damage within the warranty period, we provide a free replacement service; outside the warranty period, we can provide repair or preferential replacement solutions. Please contact our after – sales customer service for specific handling.
14. What is the compatibility of wafer cassettes with wafer equipment from different brands?
Standard – specification wafer cassettes are designed in line with industry – wide common interface specifications and can be compatible with most mainstream brands of wafer processing, storage, and transportation equipment. For special equipment requirements, please inform us in advance for compatibility assessment and customized adaptation.
15. How to properly store unused wafer cassettes?
They should be stored in a cleanroom, dry, and thermostatically controlled environment, avoiding direct sunlight and contact with corrosive substances. Special storage racks can be used for placement. When stacking, pay attention to the load – bearing capacity and stability to prevent the cassette body from deforming.
16. Can samples be provided for testing?
We can provide samples for customers to test and evaluate. The sample cost and freight will be negotiated according to the actual situation. Bulk purchases can be made after the customer is satisfied with the test.
17. Do you provide technical support and usage training services?
We provide comprehensive technical support, including product installation guidance, usage operation training, and after – sales consultation services. If necessary, professional engineers can be arranged to provide on – site technical services and training.
18. What is the service life of wafer cassettes?
The service life depends on the frequency of use, environmental conditions, and maintenance. Under normal use and maintenance, high – quality wafer cassettes can be used for 3 – 5 years; if used in harsh environments or with high frequency, more frequent replacement may be required.
19. What are the specifications to be noted when using wafer cassettes in a cleanroom?
Before entering the cleanroom, the wafer cassettes need to be cleaned twice and undergo static elimination treatment with an ion gun; when operating, cleanroom gloves must be worn, and the cassette cover should be opened inside a laminar flow workbench.
20. How does the sealing performance of wafer cassettes affect wafer storage?
Good sealing performance can effectively isolate external particles, moisture, and corrosive gases, maintaining the cleanliness level inside the cassette and avoiding quality problems such as oxidation and contamination of the wafers due to environmental factors.
21. Are the interfaces of wafer cassettes from different brands universal?
The standard – size wafer cassettes (such as 12 – inch FOUPs) of mainstream brands follow the SEMI international standard interface specifications, but some manufacturers may have customized designs. When purchasing, it is necessary to confirm the equipment compatibility.
22. How to solve the vibration problem of wafer cassettes during transportation?
Adopt a shock – absorption packaging scheme, such as adding an EVA buffer layer outside the cassette body and using shock – absorbing sponges to fix the wafer slots inside; the transportation vehicles also need to be equipped with a shock – absorbing suspension system to ensure smooth transportation.
23. What is the role of the RFID tag on wafer cassettes?
The RFID tag can record information such as the location, number of uses, and maintenance status of the wafer cassette in real – time, which is convenient for the factory to manage assets and trace, and improves the intelligent management level of the production process.
24. Can corporate logos and product information be customized on wafer cassettes?
It is supported to customize corporate logos, product models, production dates, and other information on the surface of wafer cassettes through processes such as laser engraving and screen printing, enhancing brand recognition and product traceability.
25. What are the different storage strategies for wafer cassettes in different humidity environments?
In high – humidity environments, desiccants need to be placed inside the cassette and sealing monitoring should be strengthened; in low – humidity environments, measures should be taken to prevent static electricity accumulation, and an ion generator can be used to adjust the humidity inside the cassette.
related products
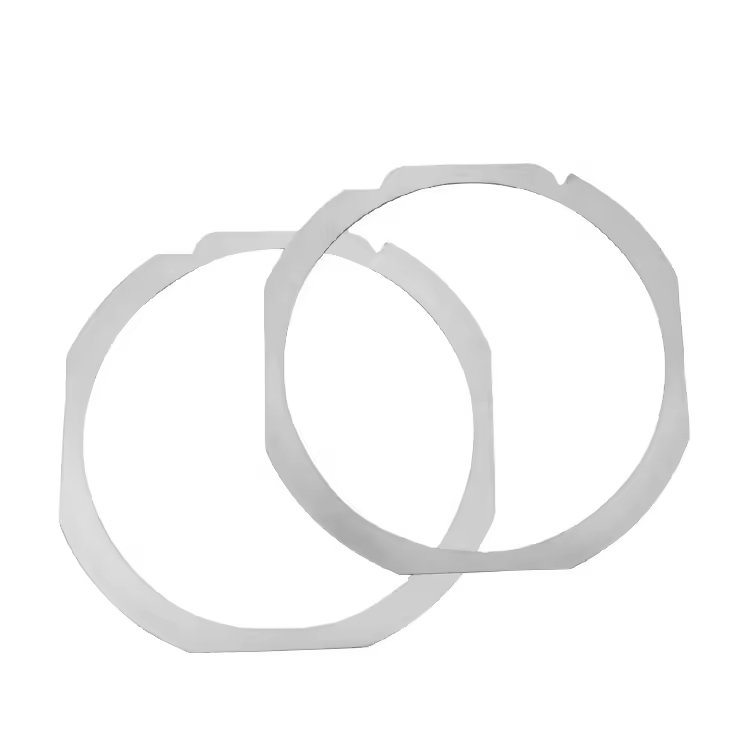
ABS Wafer Frame
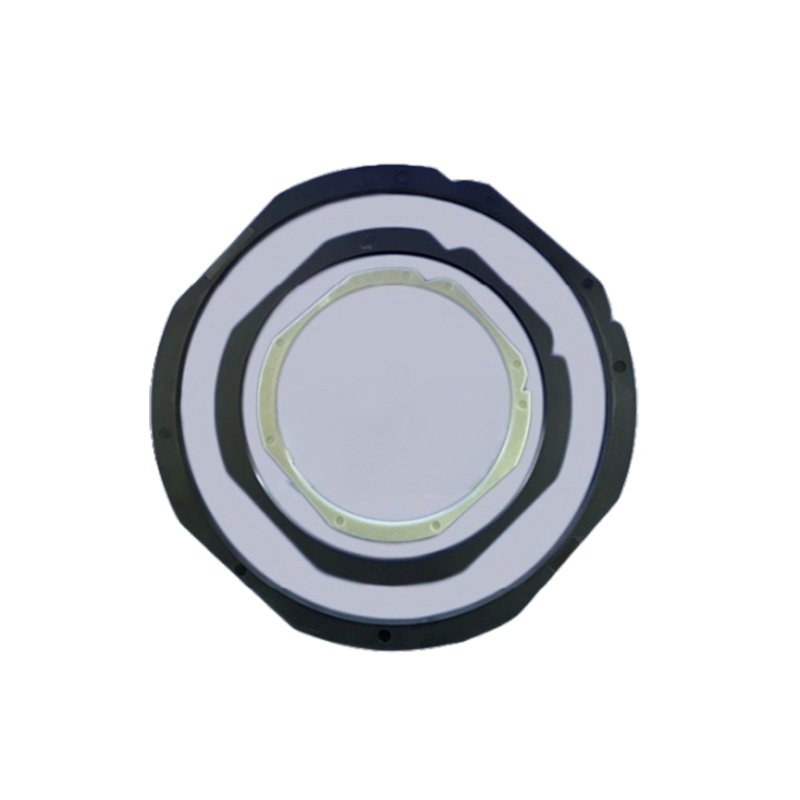
PPS Wafer Frame
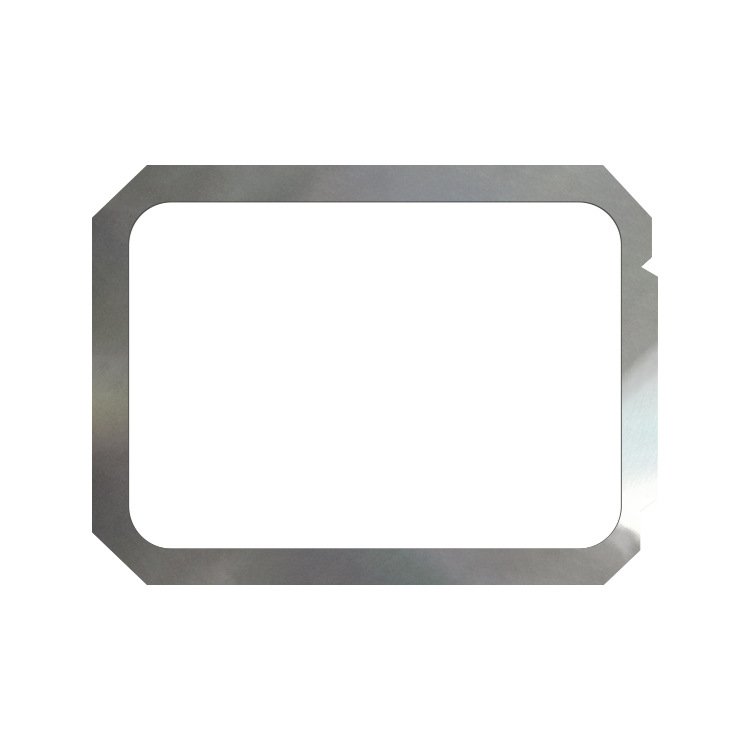
316L Wafer Ring
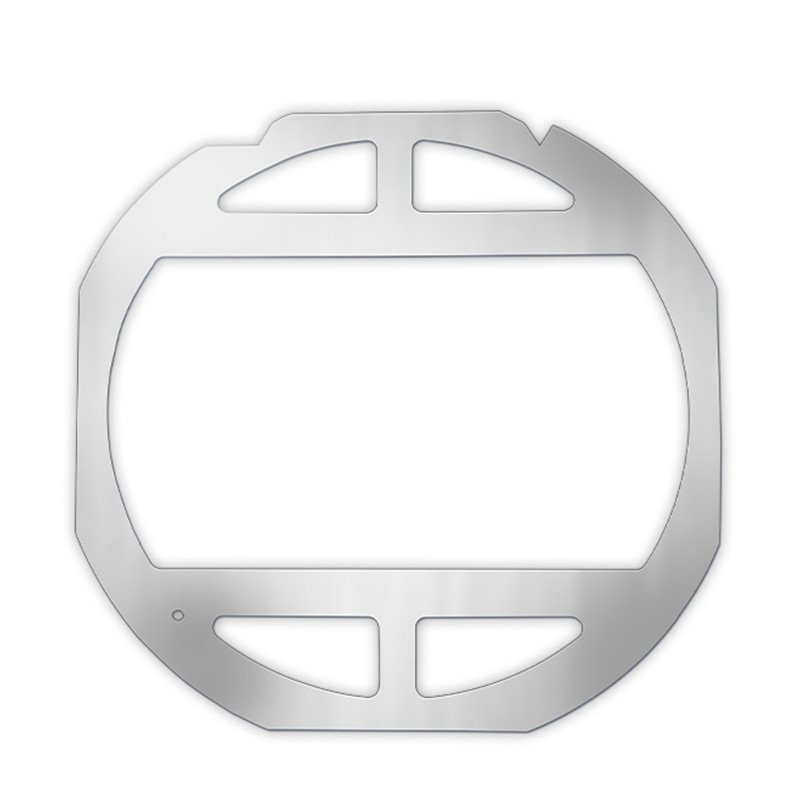
12 inches 300mm Wafer Ring Frame
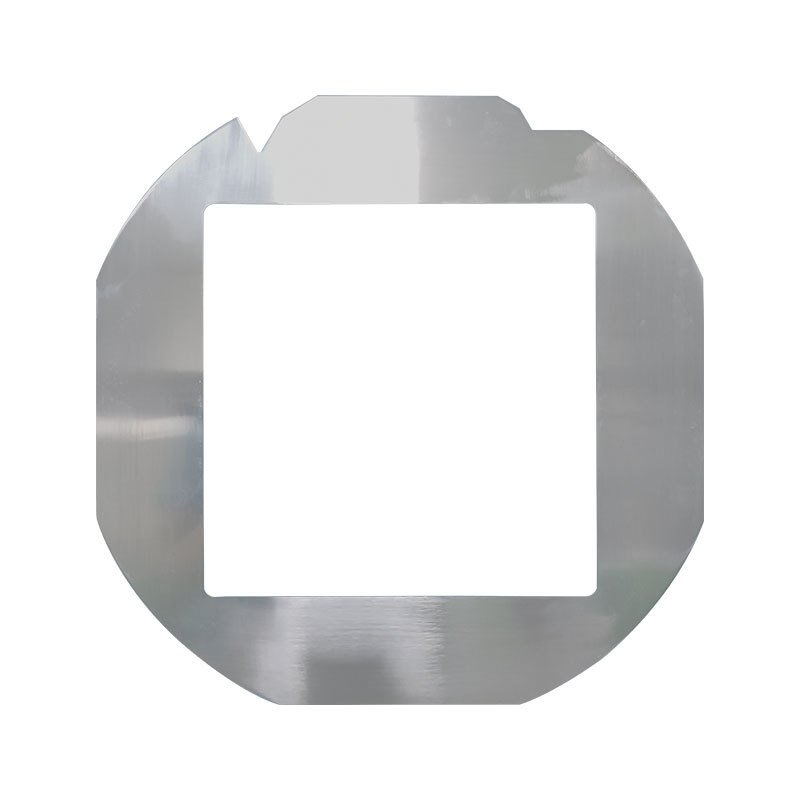
8 inches 200mm Wafer Ring Frame
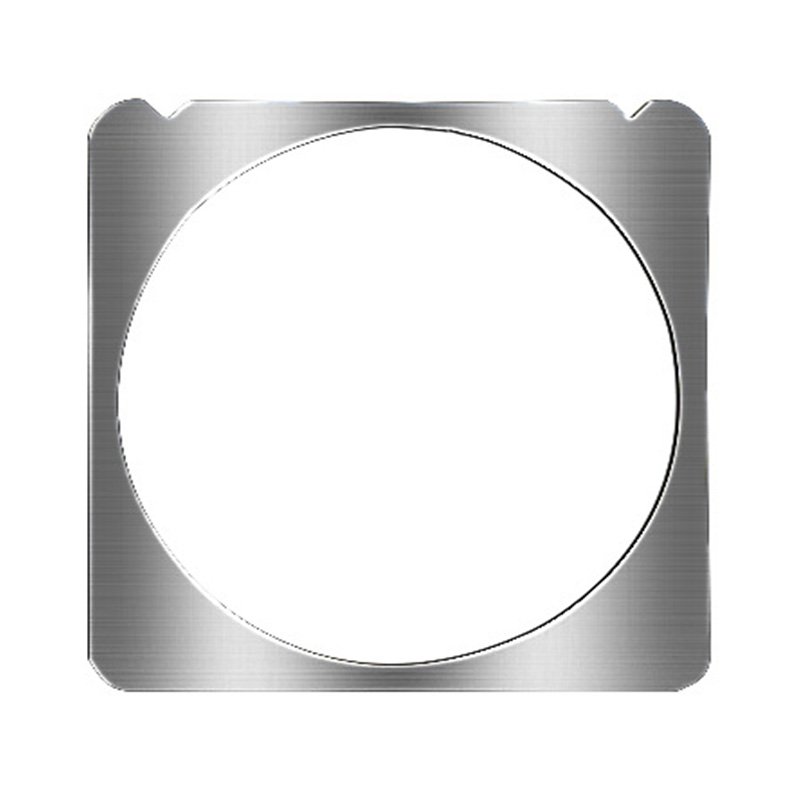
7 inches Wafer Ring Frame
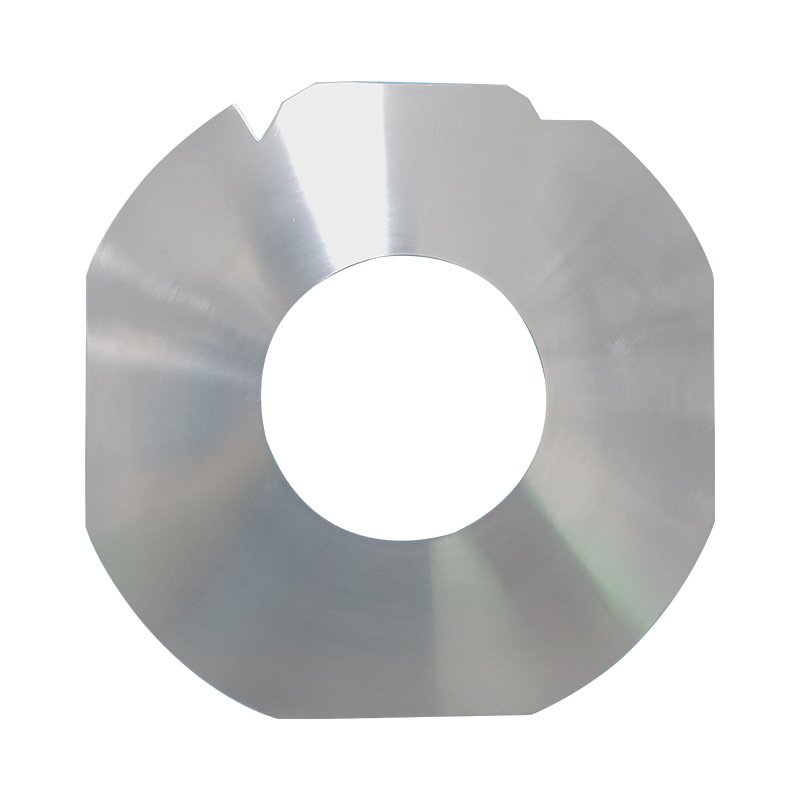
6 inches 150mm Wafer Ring Frame
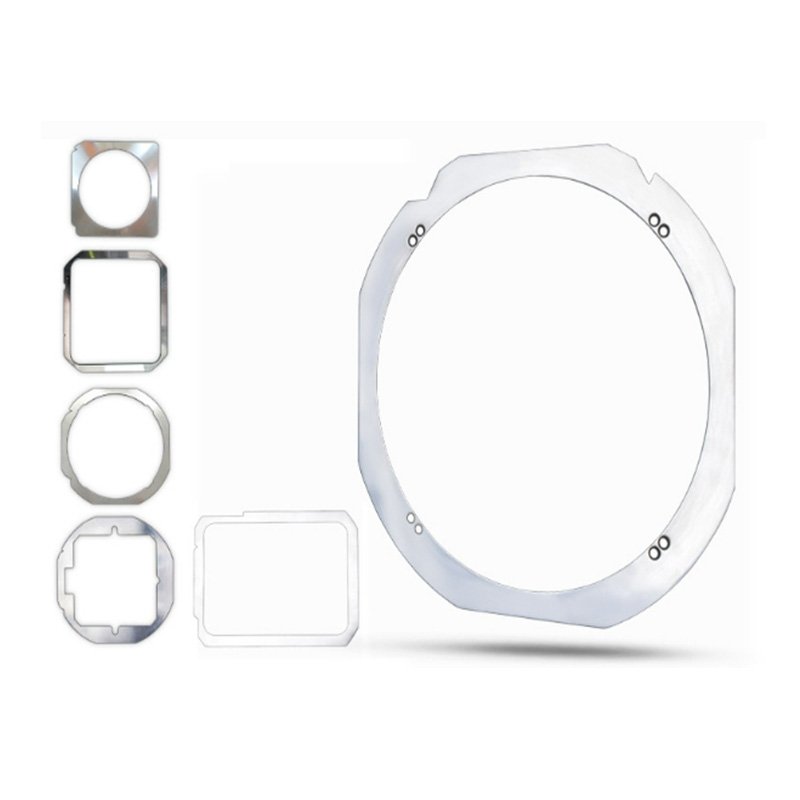